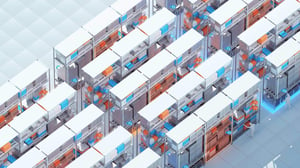
Solutions
Putaway
Putaway, once viewed as a straightforward storage task, has become a critical component of warehouse efficiency and resilience.
As businesses contend with fluctuating order volumes, tighter delivery windows, the need for greater SKU variety and more efficient returns processing, traditional warehouse processes are being pushed to their limits. The ability to swiftly and accurately put away incoming inventory, whether new or returned, impacts not only space utilization but also downstream processes such as picking, packing, and replenishment.
Optimizing the putaway process is therefore imperative, with automation the key. Selecting the right type of automation can make the difference between a good solution and a great one—or 1000 happy customers and 10,000.
OIA putaway solutions leverage both our autonomous mobile robot (AMR) and automated storage and retrieval system (ASRS) products. Through advanced robotic automation and smart software, we transform the way warehouses handle inventory placement. The result is a streamlined putaway operation that enhances overall warehouse productivity.
Types of Automated Putaway
- Inbound Putaway
- Returns Putaway
Inbound Putaway
Inbound putaway is the process of moving newly received goods from a warehouse's receiving area to their designated storage locations. OMRS and OSRS both provide efficient solutions for putaway, depending on the size of your operation. OMRS includes the Porter AMR pallet mover for putaway of full cases, while our Chuck AMR person-to-goods collaborative robot, or ‘cobot’, helps your employees put away eaches.
OSRS, our cubic ASRS solution, offers smart putaway, also known as ‘directed putaway’, to maximize operational efficiency and warehouse throughput, significantly reducing the time and effort needed to pick, pack and ship items. Smart putaway uses complex slotting algorithms to store stock in the best possible location within the OSRS grid. Using data to optimize placement of stock, OMRS minimizes the time and distance required for a human or robot picker to locate and retrieve an SKU.
Returns Putaway
With short product cycles and high e-commerce return rates, businesses need the agility to maximize sale value on returns, especially when they occur late in the cycle. OMRS retrieves information from the returns management system to help operators put away and resell returned products quickly and profitably.
Chuck travels autonomously to the pick area, then directs your workers through the putaway process, optimizing travel through the warehouse and using scans to ensure accuracy.
Chuck-based returns putaway can be implemented in weeks as part of a new OMRS deployment or in days in facilities where Chuck is already used for picking. New workers can achieve performance objectives and master exception processing within hours while improving productivity by more than 40% over manual carts, achieved by streamlining tasks, reducing in-aisle travel and eliminating long walks. Site leaders can assign putaway tasks as needed to keep the operation running smoothly.
OSRS is also fully capable of returns handling, via our induct stations. Should a stock exception arise, such as a product recall, damaged item packaging or a returned item, an operator can summon the relevant bin from the grid and then manually adjust stock as necessary. For returns, once a product has been quality checked to ensure it meets resale requirements, a human operator summons the original bin and replenishes it into the grid.
Each vs Full Case Putaway
Putaway of eaches and full cases both present distinct automation challenges.
Full Case Putaway
Typically involves handling larger quantities of the same SKU, often requiring efficient pallet or case movement to designated storage locations. OMRS excels here, using the Porter AMR to transport full cases swiftly and reduce manual handling. Once a pallet arrives at a decant workstation, Palletizer automatically unloads cases into storage.
Eaches Putaway
Sees cases of SKUs opened an the individual items stored; precision and flexibility are critical. As evidenced by Ocado Grouop's extensive experience handling eaches—including delicates and perishables—in the grocery market, OSRS is highly effective at storing eaches in its grid-based cubic ASRS.
Advanced slotting algorithms dynamically allocate storage locations, optimizing space utilization and reducing picker travel time. This versatility makes OSRS ideal for operations with high SKU variety or fluctuating order profiles. By combining OMRS for case movement with OSRS for smart, data-driven storage, OIA’s solutions seamlessly address both each and full case putaway needs.
Benefits to Automating Putaway
Inventory distortion remains a real issue in many warehouses. IHL Group estimated the global cost of inventory distortion in 2023 to be $1.77 trillion. Automating putaway reduces errors and discrepancies, and enhances inventory visibility.
OIA systems use advanced putaway algorithms, ensuring items are stored in optimal locations. This minimizes the time and distance required for human or robot pickers to retrieve stock, significantly boosting efficiency and reducing travel time during order fulfillment.
Automated putaway systems optimize warehouse workflows by minimizing manual effort, accelerating the pace of operations, and ensuring precise, efficient storage processes that maximize space and resource allocation.
Automated putaway solutions are often designed to minimize manual handling of heavy or awkward items, reducing physical strain and the risk of workplace injuries during putaway operations. And route optimization removes long, arduous and inefficient pick walks.
OMRS supports rapid and efficient returns putaway, enabling operators to resell returned items quickly. By reducing the time required to process returns, businesses can maximize warehouse space and profitability while maintaining smooth operations.
Our Putaway Technologies
Whatever your requirements, OIA’s solutions meet the challenges of handling cases and eaches, delivering unmatched productivity, scalability, and efficiency.
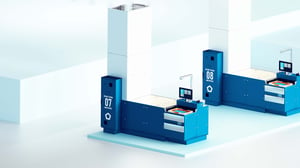
An intuitive, low-strain environment for operators to automate putaway and achieve an exceptional standard of quality, quickly and sustainably.
Learn More >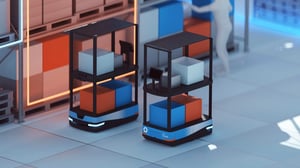
A person-to-goods AMR that helps your employees with putaway and other warehouse tasks. By guiding them through their work zones, Chuck minimizes walking, helping them to stay on task.
Learn More >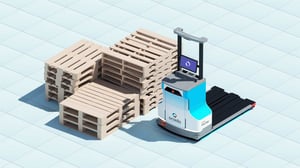
An advanced AMR for fully automated, heavy-duty tasks such as cross-dock, putaway and inventory moves, as well as collaborative each and case picking, replenishment and returns putaway.
Learn More >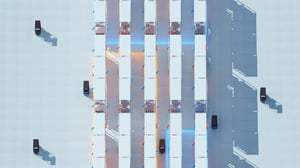
The AI-powered, cloud-native software platform at the core of OMRS. This intelligent suite of software tools orchestrates the operations of your AMR fleets in real time.
Learn More >