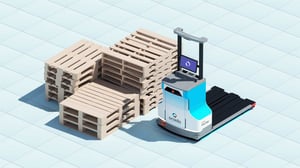
Solutions
Store / Facility Replenishment
Whether you’re a retailer, e-tailer, wholesaler or manufacturer handling single-item, full-case, palletized or caged inventory and employing one of the many different replenishment methods available, our winning solutions will optimize your B2B replenishment operations.
Replenishment is the process of restocking inventory to maintain optimal supply levels and meet demand. In retail stores, warehouses and fulfillment centers, replenishment ensures that products are readily available, avoiding both overstocks and stock-outs.
Automated replenishment leverages real-time data, predictive analytics, AI and robotics to efficiently move goods to the right location at the right time. By streamlining stock flow and reducing manual handling, automated replenishment enhances operational efficiency and improves order fulfillment speed.
Ocado Intelligent Automation (OIA) delivers high-performance ASRS and AMR-based piece and case handling systems for optimized replenishment operations. Our advanced robotics, AI-driven optimization, and cloud-based management software works together to enable businesses to scale seamlessly, reduce labor dependency, and maintain a responsive, demand-driven supply chain.
Our Replenishment Solutions
OSRS, OMRS and OCADEX are the tried and tested technologies at the core of our innovative B2B replenishment solutions.
Whatever your requirements — serving retail stores, hospitals, offices, or other mission-critical locations — Ocado Intelligent Automation’s replenishment solutions provide unmatched flexibility, scalability, efficiency and productivity for modern B2B full-case fulfillment operations.
Advanced Operations | Typical Operations
Advanced Case Replenishment
Ocado Intelligent Automation (OIA) offers an advanced automated mixed-case fulfillment solution designed for medium to high-throughput facilities, enabling seamless stock replenishment for stores and distribution centers.
Click the buttons above to view the material flows
This solution seamlessly integrates a number of our systems to streamline replenishment, from storing palletized and depalletized cases to building aisle-ready, mixed case pallets. Dense cubic ASRS storage, automated de/palletization, automated or manual pallet stores and pallet-mover AMRs all work in unison, while advanced execution software orchestrates and sequences every step.
Material flows in an OIA Advanced Case Replenishment warehouse operate as follows...
For Cases Stored in the Grid:
- A Porter AMR retrieves a pallet from inbound.
- The pallet is delivered to an Induct workstation.
- Grid robots bring empty storage bins to the workstation.
- Robotic arms depalletize cases into storage bins.
- Fully stocked bins are inducted back into the grid for storage.
For Cases Stored in the Pallet Store:
- A Porter AMR collects cases that are either too large for the grid or more cost-effective to store outside OSRS (e.g., extremely fast movers).
- These cases are placed on floor-level racking shelves for easy manual pick access.
- Stock pallets for longer-term storage are placed in upper shelves by a forklift and brought down as needed to replenish the ground-level stock.
Automated Case Picking from the Grid (Palletizer Arms):
- Grid robots retrieve cases from storage and present them at a Pick workstation.
- A Palletizer robotic arm picks and places cases onto a pallet.
- A Porter AMR transports the built pallet to the outbound pallet zone for dispatch.
Manual Case Picking from the Grid (Pick Workstation):
- Grid robots retrieve cases from storage and present them at a Pick workstation.
- An employee picks and places cases onto a pallet.
- A Porter AMR transports the built pallet to the outbound pallet zone for dispatch.
Manual Case Picking from the Pallet Store (Porter AMR):
- For cases that are too large for the grid or more cost-effective to store outside OSRS (e.g., extremely fast movers), employees manually pick them directly onto a pallet carried by a Porter AMR.
- The Porter AMR is routed by software to another employee in a different pallet store zone for further picking.
- Once the pallet is built, the Porter AMR transports it to the outbound pallet zone for dispatch.
Combined Method for Consolidating Stock from Different Storage Areas:
- An order may begin with manual case picking from the pallet store using a Porter AMR.
- The order is then taken to an automated or manual OSRS Pick workstation to complete the pallet.
- Once the pallet is fully built, the Porter AMR transports it to the outbound pallet zone for dispatch.
Advanced Operations | Typical Operations
Ocado Mobile Robot System
Person-to-goods AMRs offer a dynamic, medium-throughput solution for replenishment, with ‘cobots’ working alongside your employees to reduce in-aisle congestion by expediting replenishment tasks.
OIA’s range of OMRS person-to-goods AMR solutions, including Chuck and Porter, provide flexible replenishment for 3PLs operating smaller distribution centers. Designed for lower to medium throughput within existing infrastructure, these AMRs help maintain stock availability, preventing short-ship issues and ensuring reliable fulfillment for clients.
Chuck is ideal for lower-volume needs, while Porter supports higher throughput operations. Powered by OIA’s FES software and supported by the Mobile Fulfillment App (MFA), these intelligent systems optimize workflows, enabling efficient, scalable replenishment without costly infrastructure changes.
- An employee places cases for replenishment onto the AMR
- The AMR autonomously carries cases to the pick area for case replenishment. The employee is directed to the first task.
- The AMR directs the employee through replenishment, reducing walking and ensuring accuracy.
- The AMR sends a confirmation and any exception information to the orchestration software, and the employee moves to the next task.
- If required, cases can be picked to pallet and moved via a pallet-mover AMR
Key Benefits
Automation streamlines the entire replenishment process, from receiving and storing cases of stock to picking, palletizing and shipping. The result is cheaper and faster fulfillment of orders on-demand and a more responsive supply chain.
Constant analysis of replenishment frequency enables highly informed demand forecasting over replenishment workloads. Integration with leading WMS, ERP or OMS software enables fully automated order management—taking into account a range of factors, which might combine lot size and historical throughput with fluctuations in demand, seasonality, and market trends.
Both eaches and cases can be supported within the same site, providing the ability for retailers to replenish stock in smaller unit sizes if whole cases aren’t required. Retailers might also offer consumers the opportunity to buy products in bulk by storing a mixture of cases and eaches of the same SKU.
Automating replenishment tasks such as inducting, picking and palletizing reduces the need for human involvement, and with it the risk of injury in dealing with stock or machinery. This provides a safer, more healthy environment for your workers.
Cubic ASRS supports ambient, chill and frozen, with the ability to store products at different temperatures or select a single temp. High density storage also means refrigerated area is significantly reduced compared to manual shelving, requiring less energy. Unused space in refrigerated areas can be used to store ambient stock in busy periods; items can be transferred from grid to grid automatically.
Cubic ASRS and AMR technologies integrate seamlessly with your existing warehouse infrastructure, both hardware and software. These solutions are also innately scalable, either by adding more robots or more infrastructure.
Mission-critical replenishment needs a solution that won’t grind to a halt should a subsystem fail. Prioritize resilience or cost, based on your business needs. Both AMR and cubic ASRS systems can be configured with no single point of failure—a broken robot or pick station can be decommissioned while the rest of the warehouse continues to operate at near-full capacity.